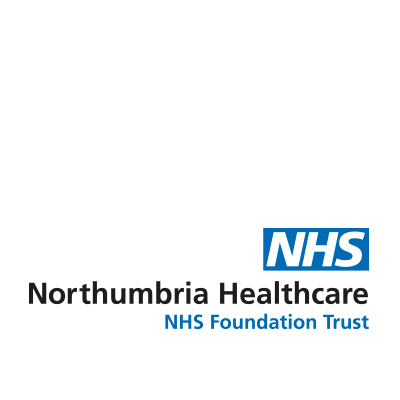
-
The trust responded to severe PPE shortages,
-
Worked with manufacturers to produce gowns
-
Built on relationship with local community and businesses
Background
At the height of the first wave of COVID-19, personal protective equipment (PPE) for NHS staff was in short supply. At Northumbria Healthcare NHS Foundation Trust, stocks dropped to around thirty gowns. The trust was using around 500 gowns a day, so looked for local solutions to bolster the supply of gowns at the trust.
In a collaboration with industry experts and major textiles manufacturers – including Barbour – the trust has produced around 1.2 million gowns and has no plans to stop there. They are now looking at how they can invest long-term in the UK’s ability to produce PPE locally and supply to other trusts across the area.
Setting up a network
Northumbria Healthcare found themselves in "dire straits" in terms of supply of isolation gowns, explains Paul Dunn, the trust's director of finance, so when Sarah Rose, a consultant on manufacturing PPE offered to help, they jumped at the opportunity.
Sarah explains the role she played in the initiative: "I was familiar with [PPE] in terms of the raw materials that are needed, and I could reach out to suppliers and factories that I know around the world and within the UK to come on board and help us with this quite quickly".
It soon became clear how many gowns would be needed, so Sarah helped set up the network of factories and within three weeks the group had opened a factory and begun training staff to make the gowns. Paul explains that they had staff who had previously worked as machinists who volunteered to help, and other local people who were furloughed or had recently lost their jobs stepped in too. Eventually, they had a network of 20 factories working to produce gowns, with a total of around 400 machinists working around the area.
Sarah explained that "the UK has lost a large amount of textile manufacturing, but [this initiative] shows they’ve been able to turn that back on very quickly and support the NHS."
Innovating in a crisis
Paul describes how "all the trusts got an email at one point saying there was such short supply. that you could basically use a plastic apron, and we felt that was a step too far".
The Health and Safety Executive (HSE) have been involved throughout, as the trust has gone through the process of developing a COVID-19 specific 'isolation' gown. Paul explains: "that's been an evolving specification. We finally got sign off from the HSE in August, and that's been difficult at times because we’ve gone around a few iterations around the testing requirements of the gown". The expertise of clinical colleagues at the trust has been essential, as well as the infection control team, who have been happy with the gowns.
One objective of the trust's work is to increase the sustainability of supply for PPE, but Paul explains "part of this initiative going forward is just greater control over quality standards". Now, he adds, "if you said that we can't use [the gowns] any longer there'd have been an uproar because they perceive them to be a far greater quality than what we’ve historically been receiving".
Expanding the initiative
Paul explains that they involved the NHS England and Improvement regional team and secured funding to expand their initiative: "we've covered the north east and Yorkshire, about 40 trusts I would say". Sarah adds, "Almost every day that goes by we’re asked if we can help in other areas".
As things have started to return to normal, some of the volunteer machinists have returned to work, and some factories have returned to their normal production lines, dropping out of the network.
Sarah describes how they filled the gaps this created by bringing more factories into the network and increasing capacity in their own factory to keep it running now: "we've probably created about 40 jobs [as people have gone back to work]…and we increased the numbers in the north-east in our own factory to make sure we've still got the same capacity".
The partnership will shortly be moving into a new factory, with capacity for sterilising gowns for use in operating theatres. This will allow them to create more jobs and produce more PPE. Sarah explains "what we've got to do is work with local councils and whoever it may be to create some apprenticeships to get some younger blood into the industry".
But it isn't just about the PPE, Paul says, "The whole story of COVID for me is the support from the local community and businesses and I think it's our way of paying it back. So whilst we have our own factory we’ll have a network which will support wider opportunity across the region".